Reduction of company costs
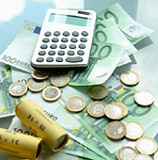
Do you need to reduce costs? We doubt there is a company management around that would give a negative answer to this question. Who wouldn’t want to achieve higher profits given current prices, or gain a larger market share thanks to lower prices! However, this seemingly trivial task is far from easy. There are many types of costs with various potential for savings. There is also one justified question: will the reduction of costs lead to poorer product quality, the extension of delivery deadlines or other phenomena that will result in lower sales?
Cost reduction projects must be approached coherently despite their importance and continual currency.
Objectives in cost reduction
The basis of this coherent approach is the stipulation of an objective in cost reduction. The specific objective is the obvious motivation of the management team, which may even be linked to a bonus depending on the degree of fulfilment. Benchmarking is a very useful supporting instrument for stipulating objectives.
The most complex task of the analysis is to obtain comparable data, preferably from a company with the same production programme, i.e. from the competition. It is obvious that this data is not readily available and therefore variously accurate estimates must generally be used. In companies with several production capacities, it is useful to compare costs from various localities. The results of this research should be the overall objective of cost reduction, specified into individual items.
Approach to cost reduction
One-off cost reduction
This is easier to implement, but the benefits are relatively low and generally do not have a permanent character. A typical method is cost reduction pressure through a cost budget for individual centres, whose managers must seek their own ways to economise. This task is often solved as a one-off assignment, i.e. a particular activity related to costs is deferred or limited. If this is an essential activity, it must be done anyway and thus the saved costs will appear as increased costs in a different period. However, by applying a responsible approach unnecessary activities or ways to do things more affordably can be revealed. However, the disadvantage is a lack of system and the risk of conflicts between centres.
Change in the cost management system
The limited benefit of one-off cost reduction is that the responsible managers cannot change the cost management system, which largely influences the value of costs.
The term cost management system refers particularly to:
- The manner of cost planning;
- The manner of evaluating real costs;
- The responsibility of specific persons for individual cost items;
- Material interest in fulfilling the cost budget;
- The development of new products focusing on production costs;
- Transfer price method and external price policy;
- Stipulating and updating standards for material and human resources consumption.
The benefit of this approach is the permanent nature of the savings and the improvement of corporate culture in terms of costs.
Change of the value chain
Similarly, the reduction of costs by improving their management system has limitations, therefore a majority of costs are predefined by the way the company generates value for the customer. In order to find costs savings, it is necessary to refer to the corporate strategy, which may be one of the following:
- lowest cost strategy;
- product/service differentiation strategy;
- strategy of lowest cost or differentiation in the chosen production segment.
The company must then analyse its value chain and cost drivers.
Provided services
Cost analysis as a part of one-off cost reduction, focussed on:
- economy;
- expediency;
- employee honesty.
Improvement of the cost management system
Comprehensive assessment of management accounting (controlling) and proposals of changes, including information technology support.
Changes in the value chain
Include updating the corporate strategy, analysing the value chain, determining factors that influence costs and finally proposals for changes in the value chain.